Line Bar
A wide variety of line bars are available!
- High-precision line bar that continues to deepen through superior manufacturing technology and reliable manufacturing
- Possible process consolidation
- Automatic diameter adjustment
- The best specification (customisation) to meet your needs
“Amazing Ideas / Facts!”
Line bars are used for intermittent hole processing with strict coaxiality, using a dedicated jig (e.g. The crank hole in a cylinder block)
- Consolidating roughing & finishing processes = Reduce investment cost.
- Automatic compensation mechanism = Productivity improvement.
- Special carbide body = high rigidity and stable performance.
Tooling configuration on a typical dedicated machine
Support bushes at both ends and in the middle
POINT!
Finishing with a single line bar - Process ConsolidationExcellent !
POINT!
Correction unit for automatic diameter correctionExcellent !
POINT!
The carbide main body increases rigidityExcellent !
High-precision processing with reduced deflection: Optimum body material from “deflection” analysis.
Reduced deflection by 50%
High attenuation
Background / Point for Development
Background
- It was difficult to achieve good roundness & coaxiality in the processing of intermittent hole, with conventional line bars.
- The need of expensive equipment resulted in high investment cost.
Operation needs to stop for diameter adjustment every time the cutting inserts are changed to new ones.
Point for Development
- “Unique Technology in Line Bar”:
- Micro-adjustment → Productivity improvement
- High rigidity → Higher precision
- Process consolidation → Reduction of investment
Example
Workpiece | Cylinder Block (Crank Holes) |
---|---|
Material | ADC12 |
Tool Diameter | ø55 +0.016/0 |
Cutting Conditions |
|
Coolant | Internal coolant |
Coaxiality | 7µm |
Roundness | 5µm |
Product Specification
Tool Specification
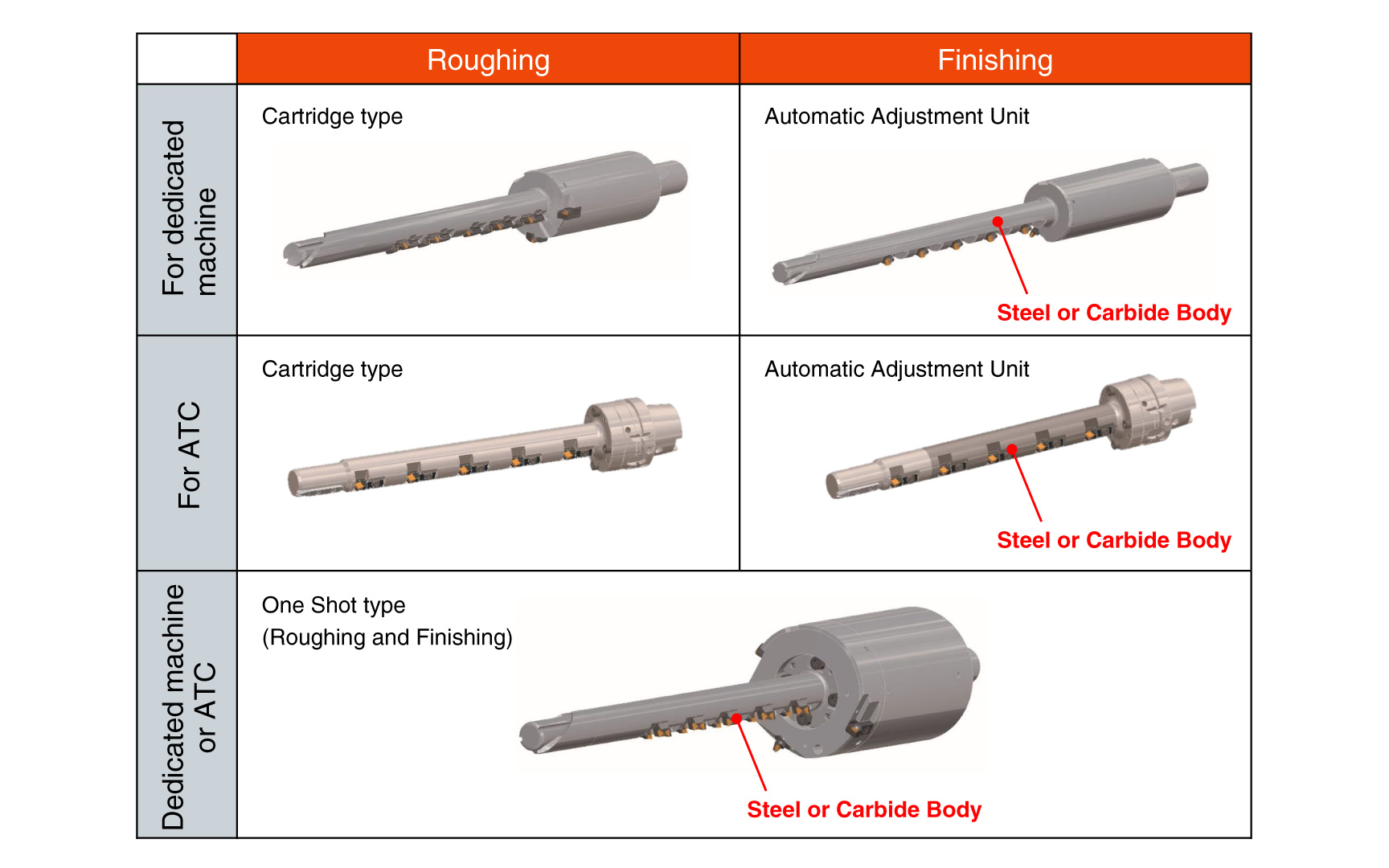
Process covered | Deep holes such as crank hole (block), cam hole (head) |
---|---|
Diameter | ø25 - |
Standard conditions |
|
Coaxiality | Within 10µm |
Example of applicable work