GB Tool (Guide-pad Boring Tool)
The Ultimate Solution for
Jump & deep Hole Reaming!
- Achieve high-precision jump & deep hole reaming with machining centers.
- The boring holders come with optimal guide pads.
- Guide pads layout contributes to high accuracy.
- Easy to operate with fine adjustment capabilities.
- Dedicated setting gauges are also available.
“Amazing Ideas / Facts!”
The GB tool consists of two rough edges and one finishing edge.
Optimal guide pad placement, tailored to resist the cutting force, allows the tool to self-guide through the machined hole, achieving excellent roundness and straightness in jump hole drilling with machining centers.
Additionally, our unique fine adjustment mechanism enables easy setting.
GB Tool Configuration
Process Sequence
Use short tools for machining the entrance. Then, use long tools for machining the back holes.
POINT!
Optimal guide pad placement, tailored to cutting resistanceExcellent !
POINT!
Fine adjustment with easy operation, Single action type for roughExcellent !
Adjustment
- ① Fix the insert with the clamping screw.
- ② Diameter adjustment with diameter adjustment screw
POINT!
Fine adjustment with easy operation, Double action type for finishExcellent !
Adjustment
- ① Secure the insert with the clamping screw.
- ② Adjust the diameter with the diameter adjusting screw.
- ③ Adjust the back taper with the adjusting screw.
Dedicated Setting Gauge
Gauge for Cutting Edge Diameter and Back Taper Adjustment
Background / Point for Development
Background
- To reduce investment and accommodate diverse production, transitioning from specialized machines to general-purpose machines is essential.
- However, performing jump hole drilling on general-purpose machines presents challenges in maintaining positional accuracy and straightness, as they lack the support provided by specialized machines.
Point for Development
- The GB tool features optimal guide pad placement, allowing it to self-guide through the machined hole. This suppresses cutting edge displacement, enabling high-precision jump hole drilling on general-purpose machines. As a result, it achieves both cost reduction and adaptability to diverse production needs.
Example
Workpiece | Cylinder Head (cam hole) |
---|---|
Material | AC2C-T6 |
Tool Diameter | ø26 mm |
Cutting Conditions | Revolution: S=2957 min-1 Cutting speed: V=260 m/min Cutting feed: f=0.1 mm/rev |
Coolant | Internal Supply, Water-Soluble 10% |
Machining accuracy |
Meets the precision requirements as shown in the table. |
Required accuracy |
---|
![]() |
Roundness / Coaxiality
Product Specification
Tool Specification
Standard conditions |
Cutting speed: V=200 - 300 m/min Cutting feed: f=0.1 - 0.2 mm/rev Internal coolant required Coolant concentration: 5% min. |
---|---|
Diameter | ø16 - (single action) ø22 - (double action) |
Example of Applicable Work
Processes | Cam Hole of Cylinder Head, Steering housing |
---|---|
Coaxiality | 8 µm |
Surface roughness | 3.2 Rz |
Diameter | IT7 |
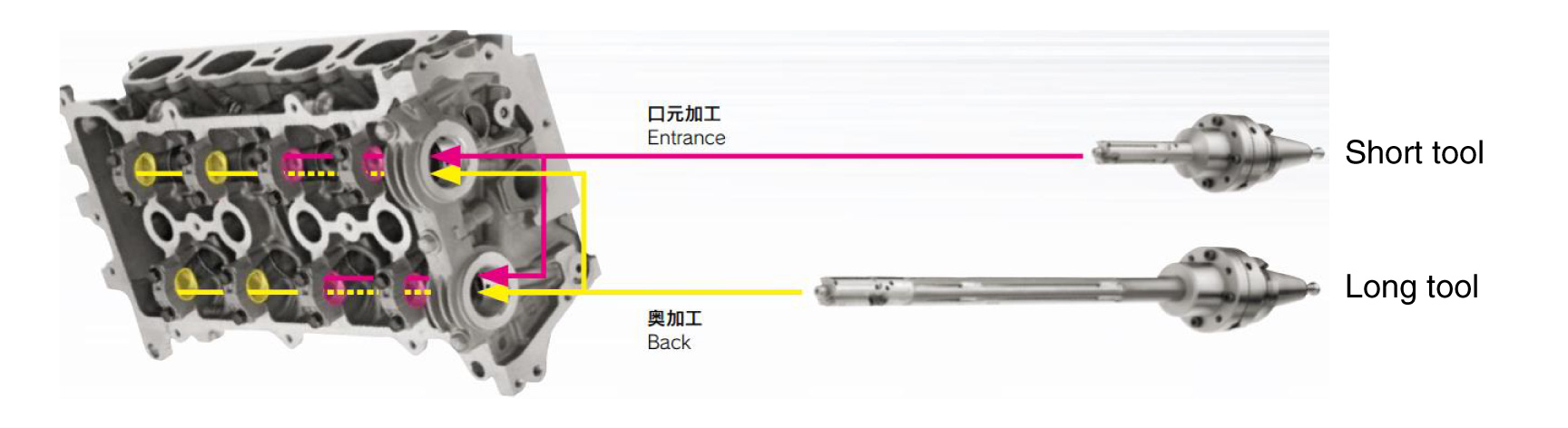